Our client, an established Original Equipment Manufacturer (OEM) in the automotive
sector, faced challenges in driving innovation, optimizing costs, and sustaining
operational excellence across multiple units. With a diverse workforce and complex
production processes, they sought a solution that could streamline operations,
foster innovation, and deliver tangible business benefits.
1. The OEM
struggled to harness the full potential of employee ideas and innovations.
2. Rising operational costs and inefficiencies were impacting profitability.
3. The need to sustain and enhance operational excellence across all units.
4. A solution that could be deployed horizontally across departments and
locations.
5. Ensuring long-term success through continuous improvement and audit
processes.
Implementation of myeNovation
1. Innovation Acceleration:
myeNovation introduced a digital platform for idea generation and collaboration,
enabling employees across departments and locations to contribute innovative ideas.
This accelerated innovation cycles and promoted a culture of continuous improvement.
2. Cost Optimization:
The platform facilitated cost-saving initiatives by providing insights into
operational inefficiencies, allowing the OEM to implement targeted cost reduction
strategies. This included optimizing supply chain processes, reducing waste, and
enhancing resource utilization.
3. Tangible and Intangible Benefits:
- Tangible Benefits: Achieved 15% reduction in production costs, 20% decrease in
inventory holding costs, and 30% improvement in production efficiency within the
first year.
- Intangible Benefits: Improved employee morale, enhanced cross-functional
collaboration, and strengthened customer relationships through innovative solutions.
4. Horizontal Deployment Process:
- Conducted a thorough assessment of each department's needs and challenges.
- Tailored the myeNovation platform to address specific requirements of different
units while ensuring a standardized approach.
- Conducted comprehensive training sessions and onboarding programs to familiarize
employees with the platform and its benefits.
- Implemented the solution in a pilot phase to gather feedback and fine-tune the
system before full-scale deployment.
- Deployed myeNovation horizontally across all departments and locations, ensuring
seamless integration and adoption.
5. Sustenance Audit Process:
- Conducted regular audits to evaluate the effectiveness of myeNovation in driving
innovation, cost savings, and operational excellence.
- Implemented feedback mechanisms to gather insights from employees, stakeholders,
and customers regarding the platform's performance and areas for improvement.
- Leveraged audit findings and feedback to make iterative improvements to the
platform, processes, and strategies, ensuring sustained benefits and long-term
success.
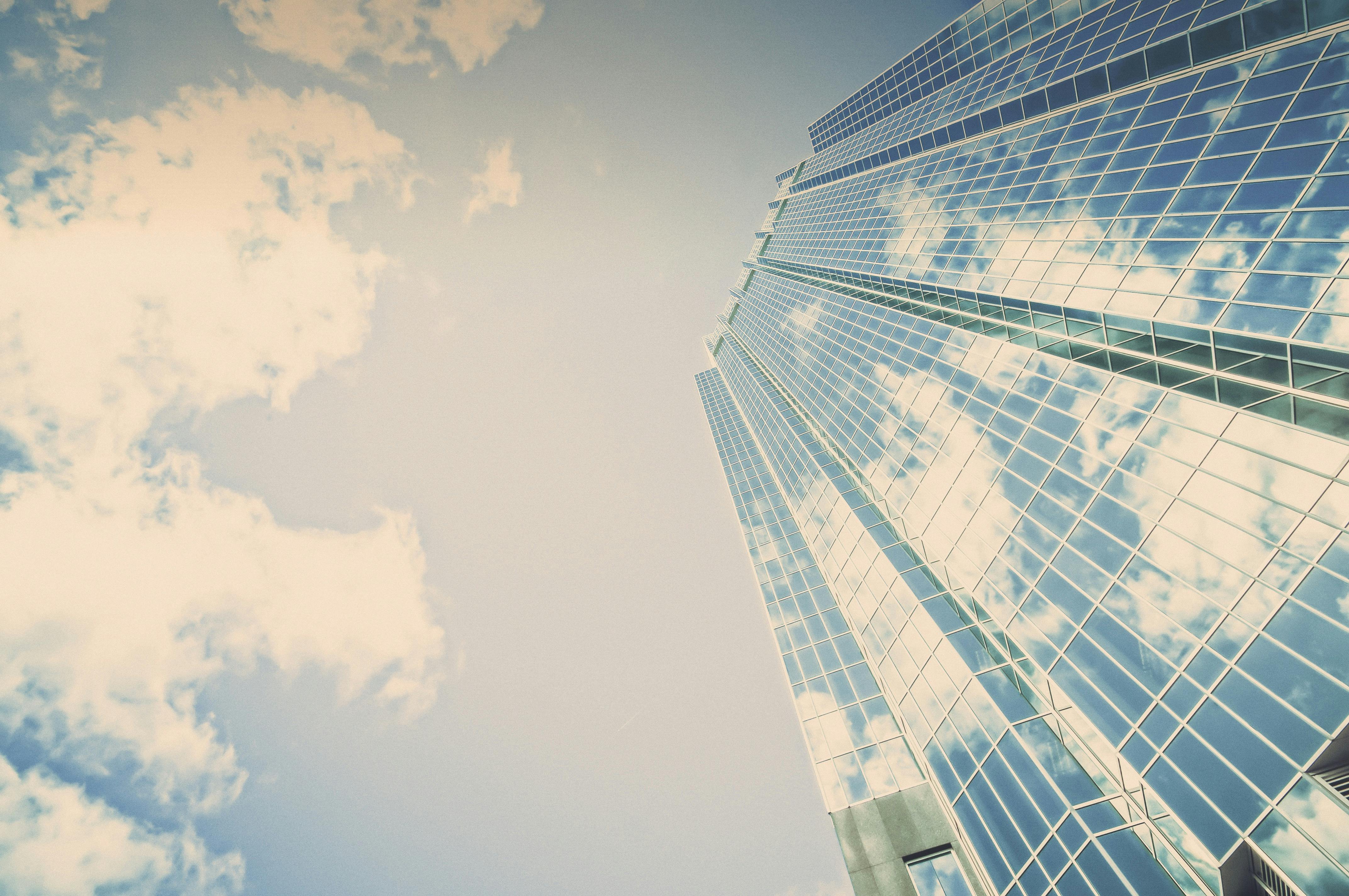
Results Achieved
1. Cost Savings: Achieved INR 97,00,000 in annual cost savings through streamlined
processes and targeted cost reduction initiatives.
2. Innovation Excellence: Increased patent filings by 25%, showcasing a
culture of innovation and intellectual property creation.
3. Operational Efficiency: Reduced production lead times by 30%, improved
on-time delivery rates by 20%, and enhanced overall operational efficiency.
4. Employee Engagement: Boosted employee engagement levels by 40%, leading to
higher productivity, reduced turnover, and improved job satisfaction.
5. Customer Satisfaction: Enhanced customer satisfaction scores by 15%,
driven by innovative solutions and improved service levels.
Conclusion
The successful implementation of myeNovation enabled our OEM client to achieve significant cost savings, drive innovation, and sustain operational excellence. By leveraging technology, fostering a culture of collaboration and continuous improvement, and implementing robust audit processes, they not only addressed existing challenges but also positioned themselves for continued growth and competitiveness in the industry.
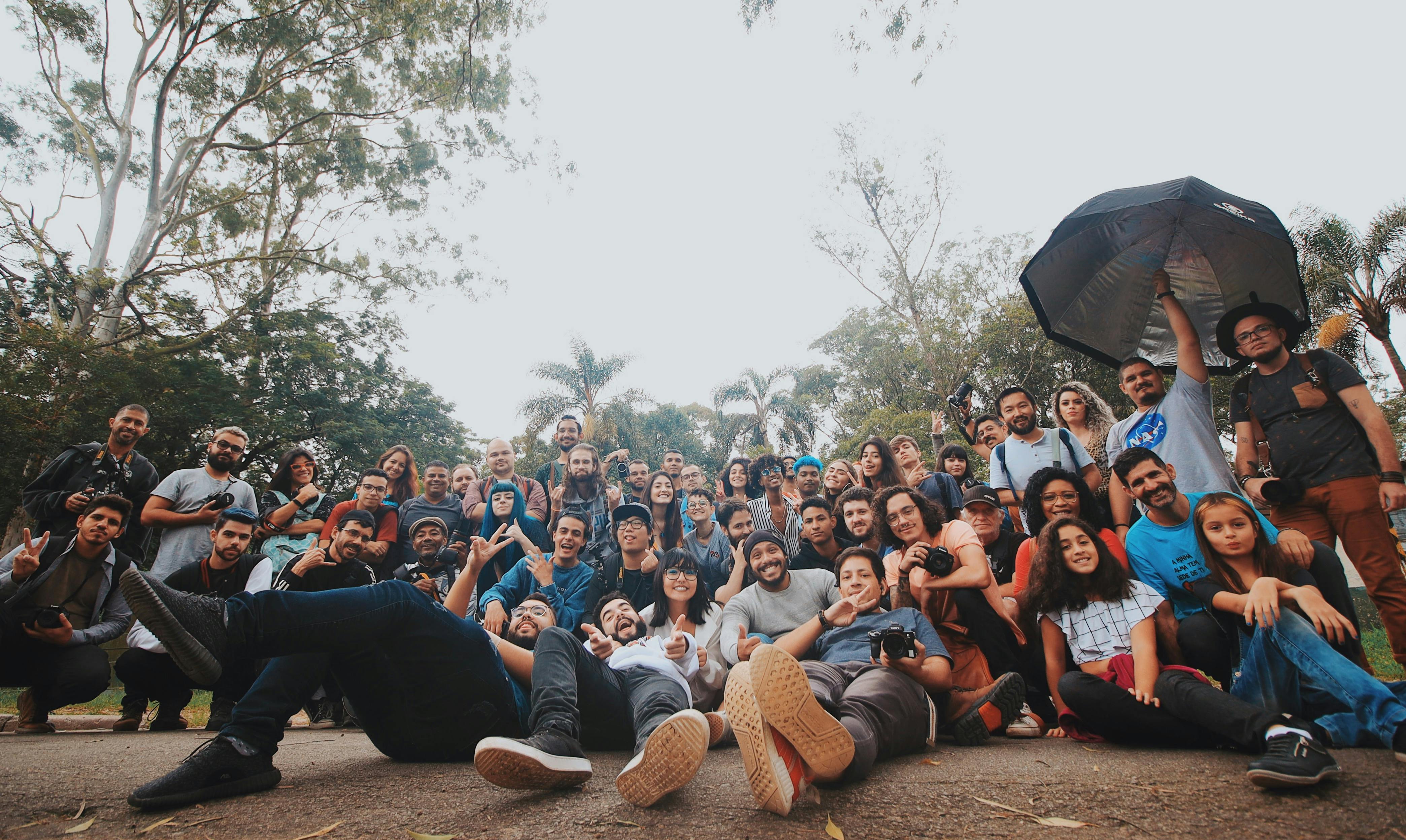